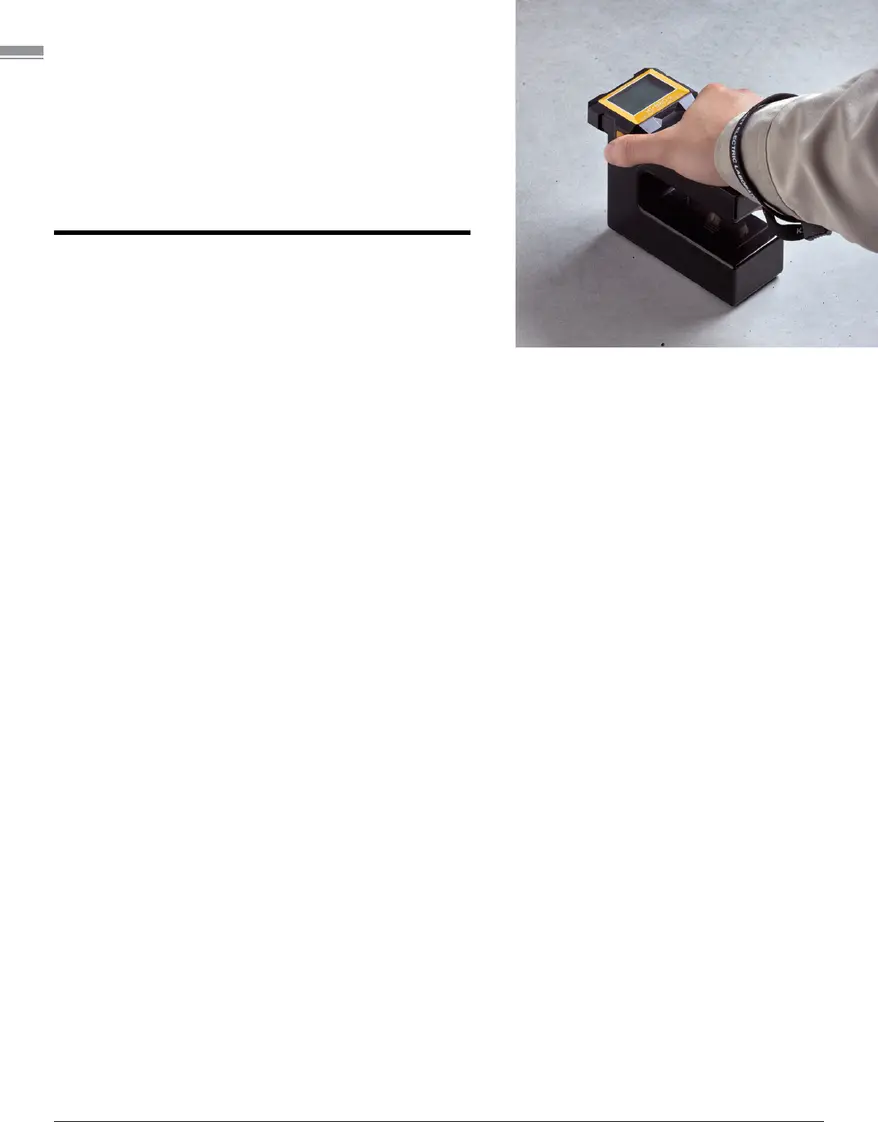
JULY 2021 www.mcsmag.com24
equipment solution
I
n the construction industry, the
quality of cast-in-place concrete
foundations, superstructure, slabs,
stairs, and architectural features, along
with the speed of project completion,
can largely depend on getting moisture
measurement right—and the same is true
with the masonry mortar used to build
brick, block, or stone walls.
Water is an essential element of both
concrete (i.e., water, aggregate, cement)
and mortar (i.e., water, aggregate,
binding material). However, at the jobsite,
everything from seasonal temperature,
rain, humidity, and groundwater to
circulating air can affect the moisture
content in concrete and mortar greatly.
This can impact setting and drying time—
and incorporating the wrong moisture
levels in concrete and mortar can be
disastrous to quality, finish, longevity,
and even safety.
Although the construction industry
has access to moisture meters, to some
extent, these tools typically require
calibration, sampling, and time. In
addition, they are not always portable or
durable enough to be used on jobsites.
Fortunately, hand-held, durable, instant
moisture measurement devices are now
available that allow anyone without special
training to spot check concrete and mortar
at the jobsite to assure that it is properly
mixed, set, and dry. In many cases,
such pre-calibrated systems allow non-
destructive, non-invasive testing on digital
displays with no pin holes or discoloration.
This approach facilitates construction
work as soon as feasible, speeds project
completion, and improves quality.
SEASONAL HEAT, MOISTURE
Concrete-water ratios can make a big
difference in the permeability of concrete,
but air humidity and summer heat also
can affect the rate at which moisture
migrates through drying concrete.
“High humidity can increase the
risk of fractures and other structural
issues. Concrete can also gradually
change from ductile to brittle when
humidity decreases, which naturally
occurs when summer heat affects
concrete’s evaporation time,” says John
Bogart, managing director of Kett US, a
manufacturer of a full range of moisture
and organic composition analyzers.
He notes that concrete cures best
between 70-80°F, so if temperatures
rise above that and climb towards 90°F,
concrete can be affected and cause surface
problems as well as reduced strength.
Hot weather, wind,and dry conditions
can increase a concrete slab’s rate of
evaporation, which can threaten the
integrity of the top layer of concrete.
Water quickly evaporates from the
surface layer, which can cause the mix
to be drier and susceptible to surface
cracking and shrinkage.
Reduced strength can also become
an issue with hot, dry weather, which
can shorten the hydration portion of the
curing process (when water is absorbed
and crystals form in the concrete). Then
the concrete mixture has less time to
hydrate these forming crystals and
create strong compressive strength. So,
concrete curing in hot weather can suffer
from limited strength and durability.
On the other hand, in wetter seasons,
excess moisture can do a great deal of
damage to concrete and its protective
coatings, as well as affect concrete-
water ratios. Because concrete is porous,
issues arise when water is trapped within
the concrete.
When it comes to structural
concrete, including foundational slabs,
construction contractors do not want to
“guestimate” moisture levels, which can
potentially jeopardize the whole project.
MEASUREMENT BENEFITS
Although traditional laboratory and online
based moisture measurement techniques
are useful in the right settings, they
have lacked the simplicity and flexibility
required for frequent spot checks
on construction sites. Because such
moisture tests are too slow, laborious,
and alter or destroy the sample, they
are not practical for the jobsite, where
concrete or mortar must stay in place.
Instead, what is needed is a fast, easy
method to determine moisture content.
So, industry innovators have developed
a simplified approach with testing
Moisture Meters
ensuring concrete and mortar
are properly mixed, set, and dry
SPOT CHECKING
By Del Williams